PHOTO
Dubai Frame. Tiqets reveals UAE winners of the 2022 Remarkable Venue Awards. Source: Tiqets
Building Integrated Photovoltaic (BIPV) are solar PV components used to replace conventional building materials in parts of the building envelope such as the roof, skylights, or facades. BIPV serves a dual purpose: as a building element and a power source that transforms building surfaces into power generating assets.
Global annual BIPV deployment is set to grow at 30 percent CAGR, from 2.2 gigawatts (GW) in 2022 to 10.6GW in 2028, according to our estimates, driven by government regulations for onsite PV on new and retrofitted buildings, along with incentives like PV generation remuneration schemes (for example, net-metering, feed-in tariff) and high electricity costs, enabling full on-site power consumption.
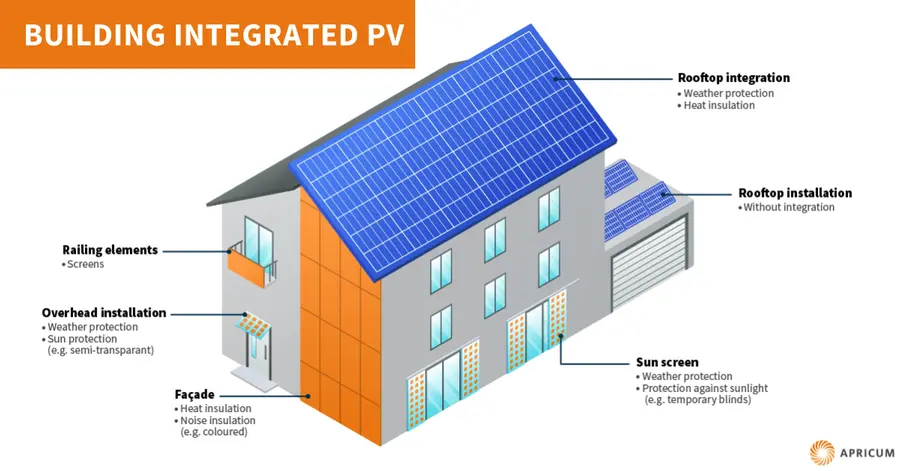
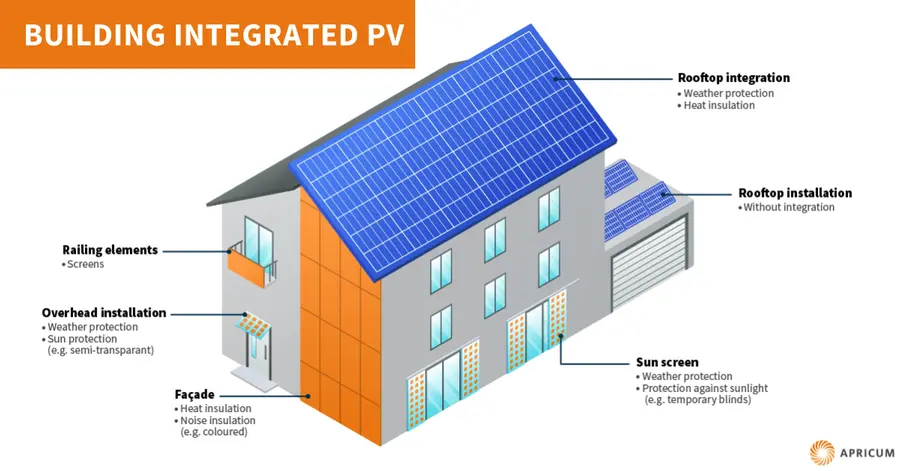
China, Europe, East Asia and North America are anticipated to lead the BIPV market, with annual installations exceeding 1 GW in each region by 2028. All regions are in the early stages of BIPV deployment, expecting double-digit growth rates in the next five years. Industry players are partnering with construction firms and architects to tailor BIPV solutions to regional demands. Governments are incentivising energy efficiency and net-zero building policies through measures like tax credits, like VAT reductions, investment tax credits and subsidies (for example, capex subsidies) for new building constructions and retrofits.
However, BIPV is different from conventional PV in terms of stakeholders involved, spectrum of technologies available, pricing strategy and economical attractiveness.
Architects are one of the main stakeholders of BIPV project deployment. Other main stakeholders include BIPV manufacturers and construction contractors.
BIPV success hinges on collaboration between several stakeholders, with architects as crucial links. They ensure BIPV adherence to regional building and electrical codes, initiate ideas for building integration, and guide product selection.
Based on our observations, the success of BIPV project hinges on the involvement of all stakeholders during the building development phase rather than retrofitting. However, aligning development timelines for the building and BIPV system could be a challenge.
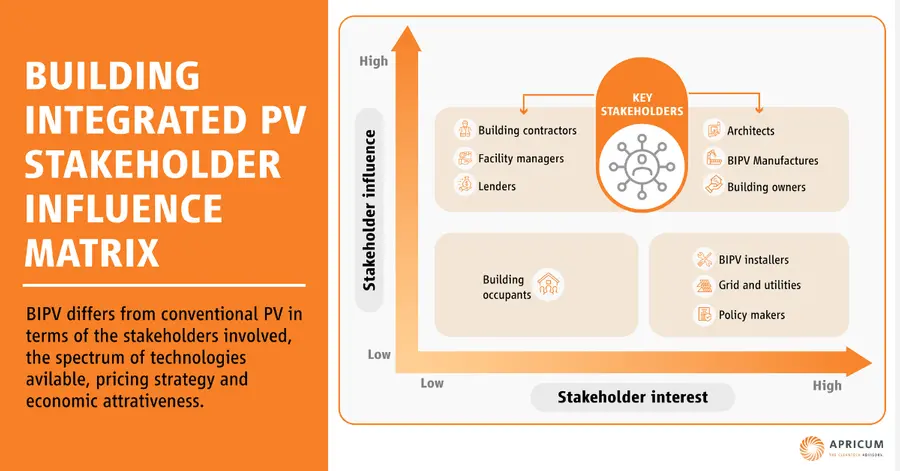
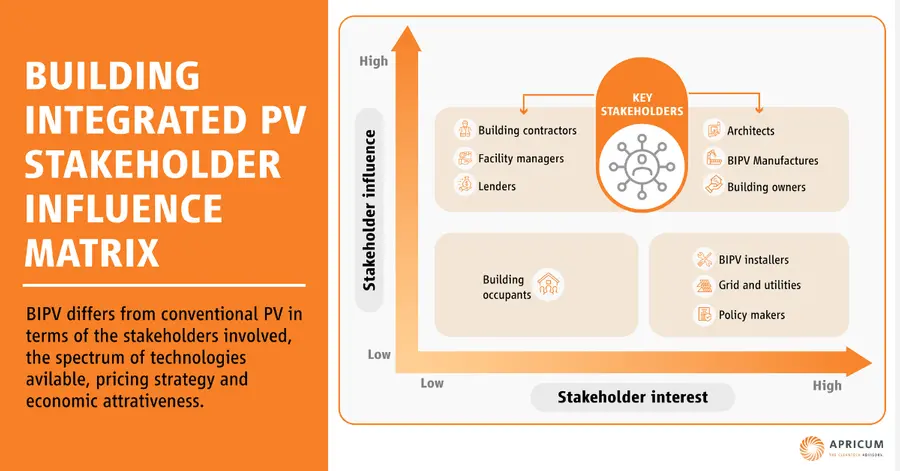
Unlike conventional PV, BIPV has a spectrum of products available from roofing to façade solution, from coloured to transparent solution. Product-customer fit depends on the customer segment.
A variety of BIPV products exist in the market. There are three main guiding parameters, amongst others, to evaluate the product-customer fit. These are:
- Building topology – roofing vs. façade (varies with geography)
- PV technology – C-Si vs. thin-film
- Cladding – Insulation and visual properties (transparent vs. semi-transparent vs. opaque)
Each customer segment (for example, small commercial buildings, car parks, multi-family apartments etc.) has their own rationale for selecting a product. This underscores the importance for BIPV module makers and architects to adopt a targeted approach in tailoring their products and services for specific customer groups.
Colouring technology enables BIPV module makers to differentiate their products for premium prices. It sets BIPV apart from conventional rooftop PV, which is seen as a commodity. Provided the concerned BIPV products are certified and meet the building and electrical codes, the premium is driven by aesthetical factors like colour and appearance) and technical factors like transparency loss, capacity.
Several module and glass manufacturers, chemical companies, construction firms, and research institutes are actively innovating with new colouring technologies to differentiate their BIPV products.
There are different BIPV colouring technologies – ceramic pigments, interference pigments and vacuum sputtering are expected to dominate the market, with their respective aesthetics, technical, and cost considerations.
Colour application to solar glass involves a concept that can be quite complex. However, the three notable colouring technologies are expected to cover >90 percent of today and tomorrow’s market.
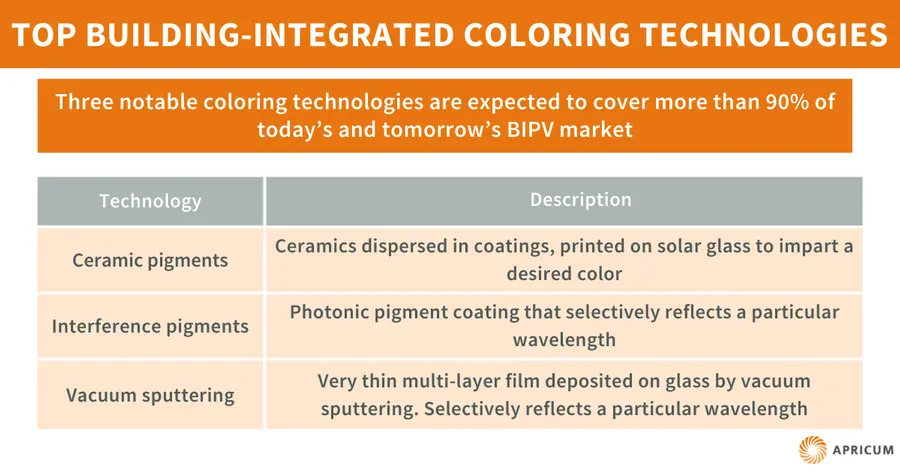
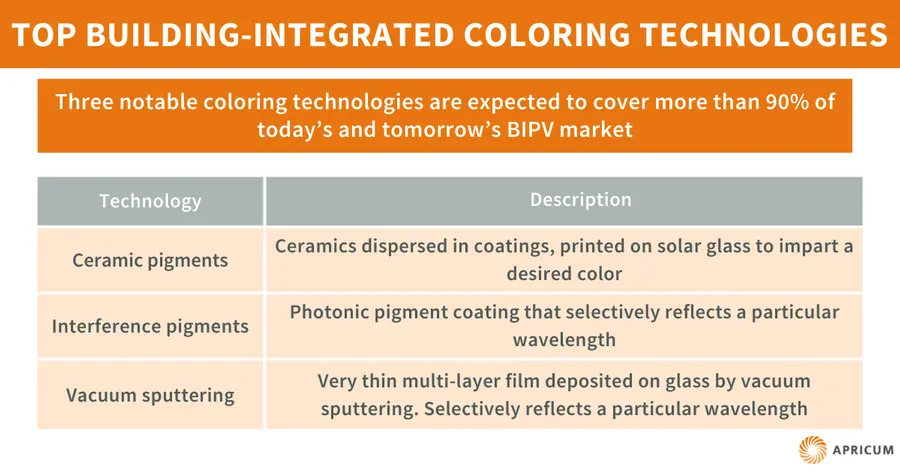
BIPV may not be widely adopted by all customer groups due to its economic viability. However, there are always customer segments that prioritise factors other than economic viability.
BIPV’s economic viability depends on several factors like building layout, envelope material savings, electricity tariffs, PV incentives, solar exposure and the transparency loss of colour technology. As BIPV systems become more standardised and production increases soon, it is expected that cost reduction will lead to improved economic viability and lower costs.
Although BIPV may not always be economically appealing, certain projects prioritise aesthetics and sustainability goals over economic viability (for example, heritage buildings).
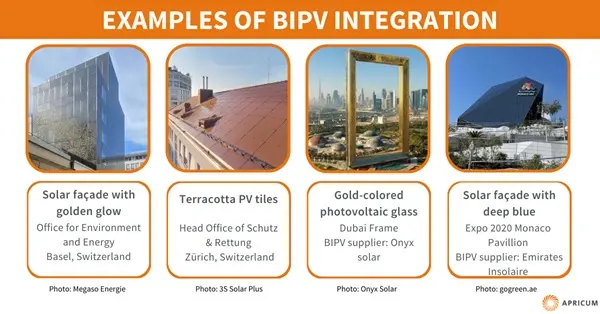
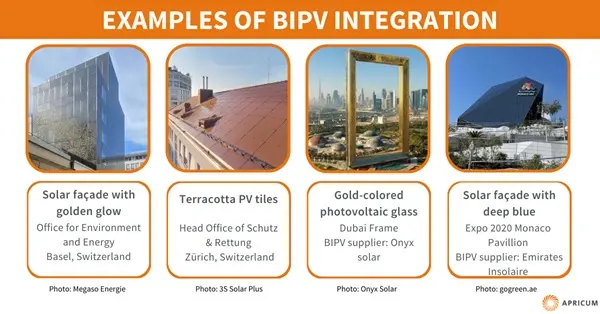
The GCC region is well-suited for iconic landmark BIPV projects. Currently, the UAE leads in regional BIPV projects. We anticipate growth in projects in Saudi Arabia and UAE, as the outcomes of Vision 2030 and COP 28 gain momentum. BIPV projects in the KSA and the GCC primarily target iconic landmark projects, with an estimated annual market size of <100 MW by 2028. These projects are expected to involve stakeholders from around the world, leveraging events like COP and EXPO, as well as locations like NEOM and Masdar City.
However, the above market size may be conservative, as we consider that regional projects might prioritise recognition over economic viability. Given the region’s abundant solar irradiation with minimal cloud cover, coupled with peak solar hours aligning with peak air conditioning usage, there is potential for economic viability through self-consumption. We anticipate that commercial buildings in the GCC, especially those subject to higher electricity tariffs and with allocated capital for sustainable building projects, to be the early adopters.
To accelerate BIPV deployment in GCC, we anticipate the following drivers:
- Develop regional expertise: Develop a local BIPV supply chain and skilled labour force to deploy projects. Currently, many projects are subcontracted to European consultants due to limited local experience, resulting in extended lead times and higher costs.
- Provide clarity on policy guidelines: Streamline building and electrical code approval processes for BIPV projects. Additionally, clarity on BIPV eligibility for PV remuneration schemes across GCC countries, where applicable
- Transition to cost-reflective electricity: Countries need to gradually adopt cost-reflective tariffs, which can justify higher initial BIPV investments, by improving the payback period.
Summary
BIPV offers a price premium over conventional PV, making it a key discussion point in the construction industry. Architects are increasingly familiarizing themselves with the concept, and module makers are partnering with construction firms to develop region-specific products. Ongoing technological innovation aims to create products with new colouring technologies that balance aesthetics, cost, and performance.
BIPV adoption requires careful evaluation for each customer segment. Tall commercial buildings are expected to be early adopters of façade solutions in most markets, while in some, residential buildings may lead due to frequent roof replacements.
In the GCC, there's a strong emphasis on landmark iconic projects. Furthermore, policy changes in KSA and UAE, such as net-zero building initiatives and cost-reflective tariffs, are expected to enhance the economic viability of BIPV in the region.
(The author is Director, Head of MENA at Apricum – The Cleantech Advisory, global transaction and strategy advisory firm dedicated to renewable energy and cleantech. Any opinions expressed in this article are the author’s own)
Subscribe to our Projects' PULSE newsletter that brings you trustworthy news, updates and insights on project activities, developments, and partnerships across sectors in the Middle East and Africa.