PHOTO
Cement plant
Ian Riley, CEO of the World Cement Association (WCA), lists improving energy efficiency, switching to low-carbon fuels and electricity, and reducing clinker in cement as the three key levers available to cement companies worldwide to reduce CO2 emissions.
"Beyond these traditional levers, the cement industry is starting to execute carbon capture and storage (CCS) projects, especially in Europe and North America," said Riley in an interview with Zawya Projects.
"The action that has the most potential to reduce CO2 emissions over the next five years at most plants is reducing clinker factor and making more use of supplementary cementitious materials (SCMs)," he noted.
Riley underlined that the challenge in implementing decarbonisation initiatives in the cement industry is not so much about funds as it is about return on investment.
"It has been estimated that to capture all CO2 emissions, an investment of 1.5 to 2 times the investment of the cement plant is needed," he observed.
Riley emphasised that regulations are crucial for incentivising quicker and more comprehensive decarbonisation. He stated that governments can promote low-carbon cement and concrete through preferential procurement policies and by revising standards to focus on performance without being too restrictive on the materials.
The WCA executive also pointed out that Artificial Intelligence (AI) is starting to play a role in optimising process control in the cement industry to reduce variability and, thus, improve quality, cost and reduce emissions.
Excerpts from the interview:
Could you touch on the 'low hanging fruit' available for producers in the region to decarbonise? What are the technologies (mature and revolutionary) that could reduce energy intensity and carbon emissions in cement plants?
Cement producers have three levers to reduce CO2 emissions that have been used to differing degrees around the world for more than 20 years. These are things that save costs as well as reduce CO2 emissions. The levers are (1) improving energy efficiency; (2) switching from high carbon to low carbon fuels and electricity; and (3) reducing the proportion of clinker in cement.
For each of these. there are many technologies. For brownfield plants, the two most important steps are:
- Switching from fossil fuels (usually coal) to waste derived fuels and biomass (called alternative fuels or AF). This will typically require some modifications to the plant to allow larger pieces to be burned more completely and there are a number of new equipment innovations that have allowed cement producers to increase their usage of AF.
- Increasing the proportion of supplementary cementitious materials (SCMs) in cement and reduce the portion of clinker (the clinker factor). Fly ash from coal-fired power plants and slag from blast furnaces have long been used as SCMs. More recently calcined clay has become a more popular SCM. Unlike fly ash and slag which are by-products of industrial processes that are in decline, clays are plentiful and found in many countries around the world.
In addition to the above, greenfield plants can take full advantage of the latest high efficiency technologies to reduce energy consumption. Today’s plants have at least 20 percent better fuel and power efficiencies than those that were built 25 years ago.
Beyond these traditional levers, the cement industry is starting to execute carbon capture and storage (CCS) projects, especially in Europe and North America.
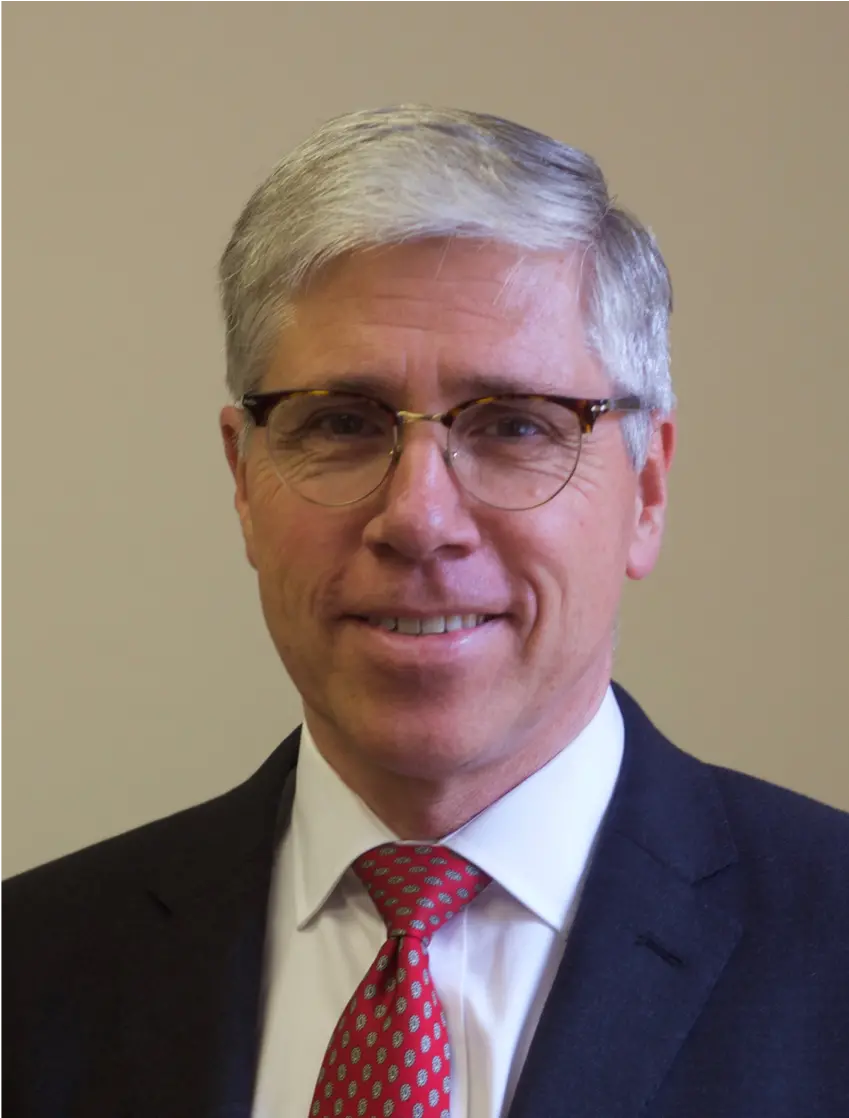
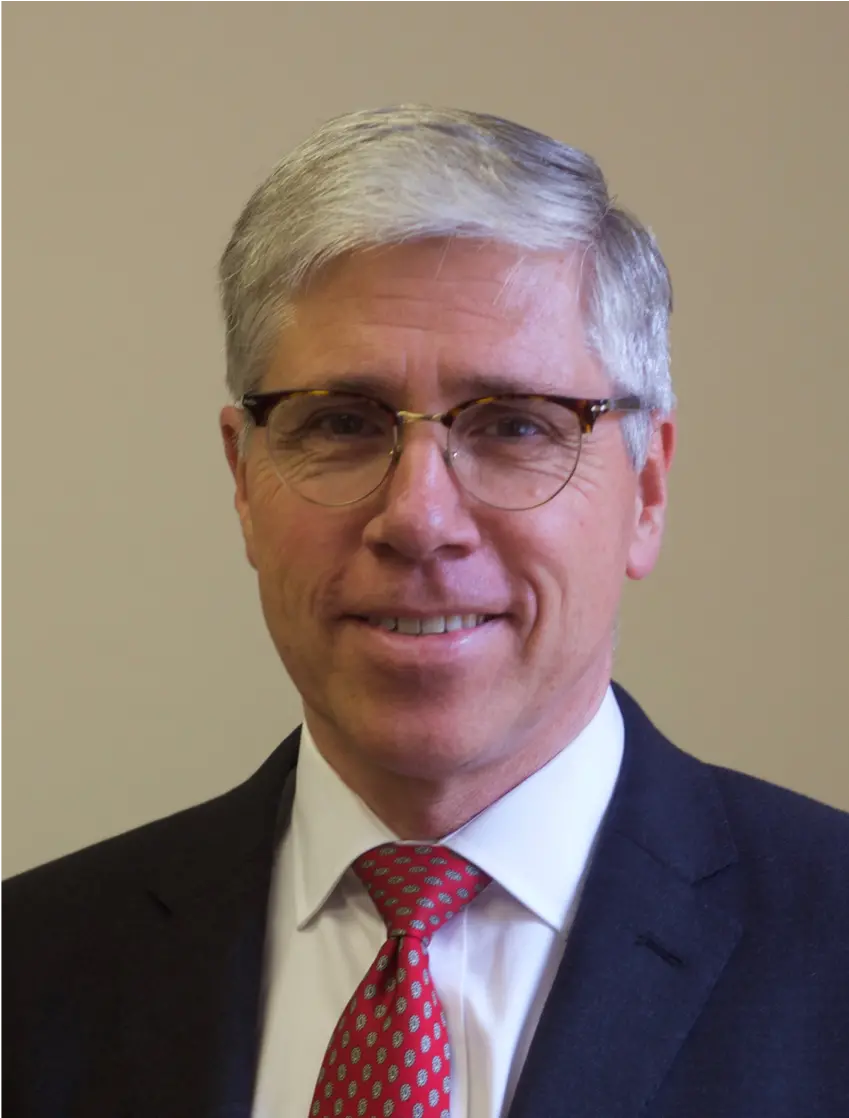
Could you elaborate on challenges faced by the industry in getting funds for decarbonisation initiatives?
The issue is not so much the availability of funds; it is more the return on investment. It has been estimated that to capture all CO2 emissions, an investment of 1.5 to 2 times the investment of the cement plant is needed. Even in regions with high carbon pricing, the return on investment only makes economic sense with large government grants. In addition, CCS projects take a long time to realise, with seven years being typical between project announcement and commissioning.
What kinds of incentives do cement manufacturers require to facilitate the decarbonisation process? Additionally, how can governments contribute to emissions reduction in the cement sector through policy and regulatory measures?
Regulation is critical in creating incentives to decarbonise more quickly and completely. While it is possible to discharge CO2 into the atmosphere at no cost, this will continue to be the most economically attractive option. The government should introduce carbon pricing schemes and ensure the carbon price is high enough to drive change.
There are two other important roles that governments can play. The first is to create a market for low-carbon cement and concrete through preferential government procurement policy. The second is to push forward revised standards that focus on performance and are not overly restrictive on the materials that can be used. Cement and concrete product standards are a major brake on progress in many countries worldwide.
From a scope 3 perspective, how are emissions within the cement supply chain, including transportation and distribution, being actively managed and reduced?
Scope 3 emissions are relatively small for cement companies because Scope 1 emissions are so large. However, as our customers focus on their Scope 3 emissions, the cement industry must do the same. The construction industry is making more use of Environmental Product Declarations (EPDs) which require a lifecycle assessment of carbon footprint including transportation and distribution. I expect to see an increasing trend towards using more local materials (for example, as SCMs) to reduce these emissions.
If you could suggest just one change to enhance the sustainability of a cement company's operations, what would it be?
In the past the technology and processes applied in cement plants was not very different for different locations. In future, this will change, and the technologies applied will be different in different locations and regulatory environments. The action that has the most potential to reduce CO2 emissions over the next five years at most plants is reducing clinker factor and making more use of SCMs.
Is it too early to ask whether AI has a role to play in cement industry in general and its decarbonisation in particular?
AI is already playing a role in improving cement operations. Firstly, AI has been applied to take advantage of the many sensors on a cement plant to identify potential equipment failures long before traditional preventative maintenance methods. This has already had some success in reducing downtime and maintenance costs. Secondly, AI is starting to play a role in optimising process control to reduce variability and hence improve quality, cost and reduce emissions.
In our previous conversation last year, you highlighted that the cement industry in the region had limited progress in reducing CO2 emissions. You also mentioned the MENA-focused roadmap developed by WCA and A³&Co to reduce the CO2 footprint. Has there been discernible progress in both areas since then?
At our annual conference on October 24 and 25 now underway in Dubai, we are highlighting some of the progress made both in the MENA region and elsewhere in reducing CO2 emissions. This will include work on the traditional levers as well as new plants that have brought together a number of new technologies to significantly improve environmental performance. We have a panel which will share their experience of overcoming the challenges and increasing the portion of AF, while another one will present new ideas on increasing usage of SCMs.
Our WCA Awards for Innovation, Climate Action and Model Plant all highlight the opportunities to improve. We have award winners from the MENA region as well as China, SE Asia and South Asia, who will share examples of what can be done and how they achieved it.
(Reporting by Anoop Menon; Editing by Dennis Daniel)
(anoop.menon@lseg.com)
Subscribe to our Projects' PULSE newsletter that brings you trustworthy news, updates and insights on project activities, developments, and partnerships across sectors in the Middle East and Africa.